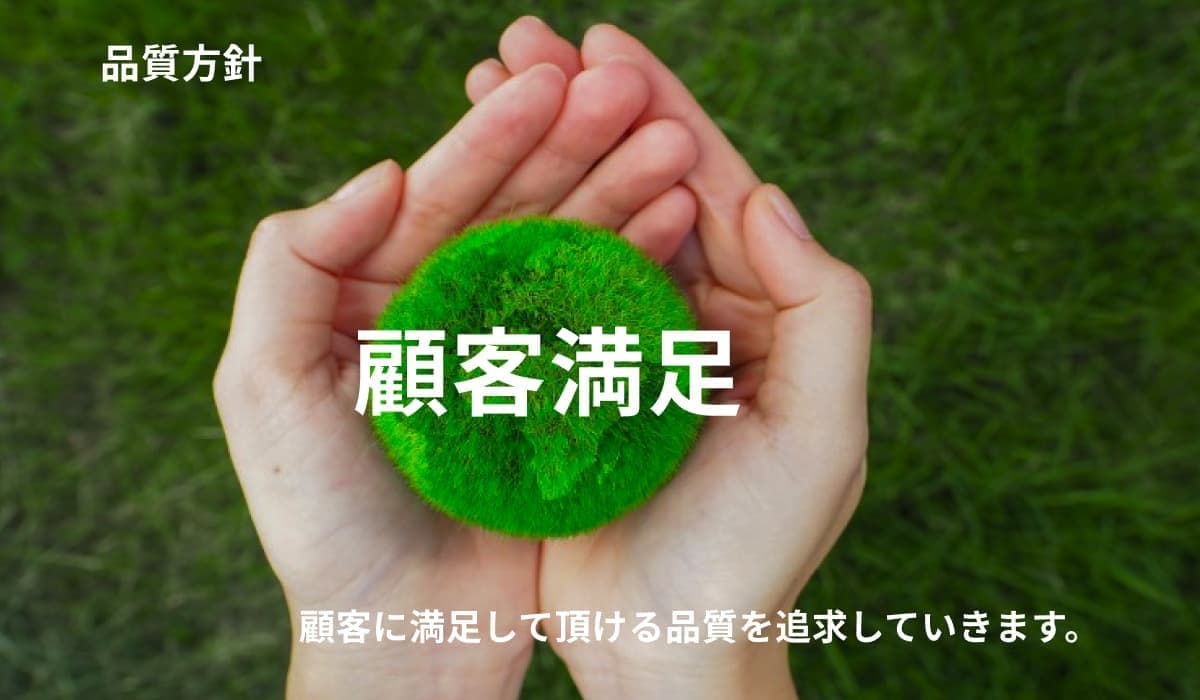
品質目標
原価低減
- 人材不足・物価高騰など製造業にとっては厳しい時代です。しかし、お客様はコストを求めますし、会社経営としても大事なファクターです。私たちは英知を結集させて原価低減に挑みます。
品質安定
- ハードルが低く見られがちですが、品質は維持・安定こそ難しく、私たちは品質の向上に取り組むことで安定という成果の獲得に挑みます。
納期短縮
- 納期短縮は生産性の向上によって成し得るものです。個々の納期短縮意識も重要ですが、自動化の促進や新たな手法考案など技術的視点での取り組みも重要です。私たちは英知を結集させて納期短縮に挑みます。
品質保証体制
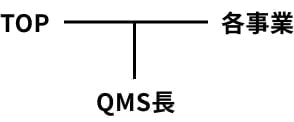
独自の品質保証体制
ISOの返還
- 弊社は過去にISO9001:2000の認証を2002年~2011年までの9年間取得していましたが、その後は返還しています。当時は、製品・組織・環境・労務など会社業務はすべて品質に通ずることであると考えて全業務をQMS対象にしていました。現在のISOが品質と環境が統合されつつありますが、それらの先駆け的な取り組みを当時から実践していたことになります。これらの取組みは高く評価され、近隣の企業から監査の要望や講義会の開催を求められることもありました。現在は認証を取得していませんが、同様のQMSを維持することで品質を保つことができると考えています。
品質保証課の廃止
- 品質保証課があるとお客様から信頼され易く、無いと不安に思われるケースが多々ありますが、弊社は過去に品質保証課を設立~廃止した経緯があります。品質保証課はお客様の矢面に立ち品質交渉などをおこなうため、品質意識が高い人材が育ちます。しかし、組織の大多数を占める製造部門の人材はそれらの機会が品質保証課の存在によって奪われてしまい品質意識は低いままでした。そのため品質問題の減少はおろか増大する傾向にありました。そこで当時、もっと全員で品質に取り組む体制にするべき、TQC・TQMをもっと向上させるべきとして廃止の決断をしています。
QMS長を特定者にしない考え方
- 弊社では部長以上の役職者をQMS長にしています。特定者にすると据え置いているだけで各事業における技術的や品質的知見に欠けて正しい判断が出来ないためです。直属の部署の部長以上はQMS長ではありません。違う部署の部長以上がQMS長を務めます。臨機応変にして的を得た判断が出来るようにしています。
弊社品質マネジメントシステムの一部ご紹介
顧客所有物管理システム
- 外部提供者の所有物に対して識別・保管・保護・防護方法を定めて適正な保管・管理をする仕組みを構築しています。
計測器管理システム
- 日常点検・定期点検、業者校正・自主校正の仕組みを構築しています。
データ分析システム
- 加工で得られた寸法や設備稼働におけるパラメータ・出力値などを集計して傾向を分析しています。品質や精度の向上・設備の有効利用や省エネ・生産性の向上・新規案件へのノウハウなどとして様々な場面でデータ分析した結果が活躍しています。
検査員認定制度
- お客様独自で認定制度をお持ちで運用を求められる場合には準拠致します。制度をお持ちでない場合には弊社独自の検査員認定制度を適用して力量を図り、一貫した方法・判断にて検査の実現を目指す体制を構築しています。
出荷検査および出荷許可システム
- お客様へ製品を納品した場合に初見で発見できる問題や苦情になり得る問題は、弊社で発見できなければいけない問題であり、弊社では出荷前にそれらの状況が起こっていないか・著しくレベル低下したものを供給しようとしていないか出荷前にチェックする仕組みと権限者による出荷許可の仕組みを構築しています。
加工請負業にしては品質意識が高い理由
加工請負業の品質意識が低い理由
- 取り扱うものが自社製品では無いことが根本要因ですが、加工請負業は従来、実作業工数に対して単価で取引する場合が多くライバルもひしめく業種であるため価格競争に陥り易い。実作業以外の人的・物的・財政的資源を確保して単価へ上乗せることが難しいため、品質は二の次、社風もコスト重視になりがち。品質や技術向上に必要な投資が難しいため適切な教育訓練や検査体制が整わず人材のスキル・意識不足や既存の生産方法に依存して変革が起こらない状況になります。また、その状況でありながら利益向上や納期対応は必要とされるため品質は作業者個々が元々持っているスキルに委ねられ、長時間労働や生産効率へのプレッシャーなどもありミスが誘発する状況を招き易くなります。弊社でも過去似た傾向がありました。しかし、その体質のままだと信頼を失い仕事が無くなります。そのため、弊社では早い時期に変革が起こっています。
毎日1000種類発生する不良をゼロへ
- 自動車部品の製造を主体にしていた時代にお客様との取引において不良品流出20PPM(100万個中20個)以下の目標がありました。成形品など同じ1つの商品を大量生産して納品する会社は1つの商品だけで20PPMを目指せば良いですが、弊社の場合はそれらの部品(当時部品点数300点以上)を使用して半田付けや組付けなど幾つもの工程作業を行うため、購入品・外注・自社工程すべての品質を管理しないと達成できないとても過酷な目標でした。当時は毎日1000種類の不良が発見され流出して客先の工程で異常が見つかり毎日客先に訪問してライン在庫の選別をしていました。それらの打開策として品質保証課(当時は技術課)を立ち上げ、1000種類の発生をゼロにするため取り組みを始めました。毎日1000種類の不良をすべて分解・解析して原因を突き止め対策を討ちました。購買不良は購入先と一緒に原因や対策を話し合って解決していきました。外注不良は外注先を定期的に廻って作業員全員と直接話し合う場を提供してもらいました。社内外含め異常連絡方法や作業者認定制度・初期流動管理など新たな手法を取り入れていき品質意識の向上と仕組みの構築に取り組みました。次第に効果が表れ日々発生していた不良は徐々に減少してゼロになる日が訪れました。客先が取引している300社中3社が選出される品質賞を受賞することになりました。
大手セラミック会社の監査過去最高得点
- 大手セラミック会社様との取引をはじめる前に立ち入り監査を受けました。日本にてISOの解釈がまだ深く浸透していない時代だったため、解釈の違いによって求める管理の在り方について思想の違いがあり意見の食い違いも多少ありましたが終始建設的に進み、最終的には100社以上の数々の加工業者を監査してきたけれど過去最高得点ですと言って頂ける監査結果を得ることが出来ました。現在も取引を続けさせて頂いています。