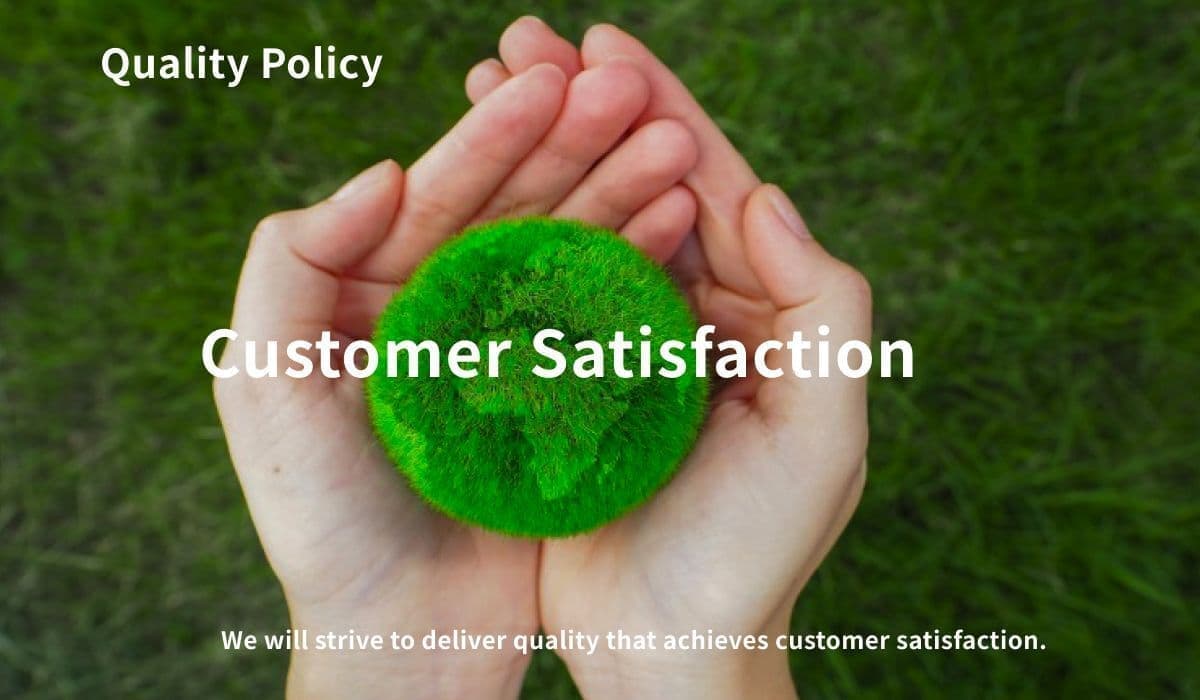
Quality Objectives
Cost Reduction
- During these difficult times for the manufacturing industry due to shortages of human resources and price inflation, both our customers and LEAD Co., Ltd. demand reduced costs. We will pool our wisdom to challenge this issue and strive for cost reduction.
Quality Stability
- Whilst quality maintenance and stability is often underestimated, it’s a significant challenge. We address this by working to improve quality, thus achieving the outcome of stable quality.
Delivery Date Shortening
- Shortening delivery dates can be achieved through productivity improvements. While individual awareness of shortening delivery dates is important, efforts from a technical viewpoint, such as promoting automation and inventing new methods, are also essential. We will gather our collective wisdom to challenge this issue and strive for shortening of delivery dates.
Quality Assurance System
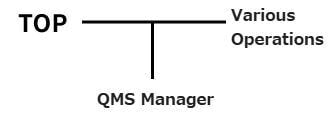
Unique Quality Assurance System
Return of ISO Certification
- LEAD Co., Ltd. held ISO9001:2000 certification for nine years, from 2002-2011, and has since returned it. At that time, we considered all company activities, including product, organization, environment, and labor, to connect to quality, and therefore subject to the QMS. While the current ISO combines quality and environment, we have pioneered the efforts since that time. Our initiatives were highly valued, and we often received requests for audits and lectures from neighboring companies. Though we don’t currently have certification, we believe we can maintain quality by maintaining a similar QMS.
Abolishment of Quality Assurance Section
- While having a Quality Assurance Section often leads to heightened trust from customers, there are many cases where the lack of one creates anxiety. However, LEAD Co., Ltd. has a history of establishing and later abolishing such a section. Quality Assurance raises high-quality conscious individuals as they take charge of quality negotiations with customers. However, the majority of personnel in the manufacturing department lacked these opportunities due to the existence of the Quality Assurance Section, keeping their quality-consciousness low. This resulted in an increase in quality problems, not a decrease. Therefore, we decided to let everybody work on quality and enhance TQC/TQM, which led to the abolishment of the Quality Assurance Section.
Concept of Not Assigning a Specific Individual as QMS Manager
- At LEAD Co., Ltd., we assign those in managerial positions above division chiefs as QMS Managers. Conferring the responsibility to a particular individual leads to the stagnation of technical or quality-related knowledge in various operations, hence hindering correct judgment. Direct department chiefs don’t serve as QMS Managers. Instead, division chiefs from other departments take on the role of QMS Managers. This flexible arrangement ensures appropriate judgments can be made.
Introduction of part of our Quality Management System
Customer Material Management System
- We have established a system for properly storing and managing materials by defining the identification, storage, protection, and prevention methods for materials owned by external providers.
Measuring Equipment Management System
- We have established a system for daily inspections, regular inspections, and calibration by professional service providers and self-calibration.
Data Analysis System
- We aggregate and analyze data such as dimensions obtained from processing, parameters in equipment operation, and output values. The results of data analysis play an active role in various situations such as quality and accuracy improvement, effective use of equipment, energy saving, improvement of productivity, and know-how for new projects.
Inspector Certification System
- We comply with the customer’s unique certification system when it is required. If the customer does not have a system, we apply our own inspector certification system to measure their capabilities and establish a system to aim for consistent inspection implementation with consistent methods and judgments.
Shipping Inspection and Shipping Permission System
- Issues that can be found at first glance when delivering products to customers and potential complaints are problems that we must be able to detect at our company. We have established a mechanism to check before shipment whether such situations are occurring and whether we are about to supply significantly lower quality products, as well as a mechanism for shipment permission by the authorized person.
Reason for the high quality awareness in subcontracting work.
Low quality consciousness in subcontracting work
- The fundamental reason is that the items handled are not our own products. Historically, subcontracting is often transacted at a unit price against actual working hours, and due to the competitive nature of the industry, it easily falls into price competition. It is difficult to reserve human, material, and financial resources other than actual work and add them to the unit price, so quality tends to be secondary, and the company culture prioritizes cost. It is difficult to make the necessary investments for quality and technical improvement, and it results in a lack of employee skill and awareness, a lack of proper education and training, and an inspection system, leading to a situation where no changes occur and dependency on existing production methods. Meanwhile, it is necessary to improve profits and comply with delivery times, so quality is left to the original skills of each worker, and the situation invites mistakes due to long working hours and pressure on production efficiency. Our company also had a similar tendency in the past. However, if we continue with this attitude, we will lose trust and have no work. Therefore, changes are being made in our company at an early stage.
Everyday 1000 defects to zero
- We had a target of less than 20PPM defective products per million in our dealings with customers when we were mainly manufacturing automotive parts. Companies that manufacture and deliver large quantities of the same item, such as molded products, only have to aim for 20PPM for that one product, but in our case, we had to manage the quality of all purchased products, outsourcing, and our own processes because we were soldering and assembling using more than 300 parts at that time. It was a very severe target that could not be achieved without managing all quality. At that time, we found and exported 1000 kinds of defects every day, found abnormalities in the customer’s process, and we were visiting the customer every day and selecting line inventory. As a measure to break through them, we set up the quality assurance section (at that time, the technical section) and started working to reduce the 1000 occurrences to zero. We decomposed and analyzed all 1000 types of defects every day, identified the cause, and discussed countermeasures. For purchasing defects, we discussed causes and countermeasures with suppliers and solved them. As for outsourcing defects, we provided a place where we could talk directly with all the workers by regularly visiting the outsourcing suppliers. We introduced new methods such as methods for contacting abnormalities inside and outside the company, worker certification system, initial flow management, and worked on improving quality consciousness and building systems. The effect gradually appeared and the defects that occurred daily gradually decreased and the day came when it became zero. We received a quality award chosen by 3 out of 300 companies trading with customers.
The highest audit score in the history of a major ceramic company
- We received an audit before starting transactions with a major ceramic company. Since it was an era when the interpretation of ISO was not yet deeply permeated in Japan, there were differences in thought about how to manage the interpretation differences, and there was some disagreement about opinions, but it proceeded constructively from beginning to end, and finally we were able to receive an audit result that said it is the highest score ever even though they have audited over 100 subcontractors. We are still continuing our transactions.
591-4, Ishigaya, Yoshiwa, Ube City, Yamaguchi Prefecture 759-0134
0836-62-1531
Dial your international access code, then 81 for Japan, then 836-62-1531 while omitting the leading ‘0’.